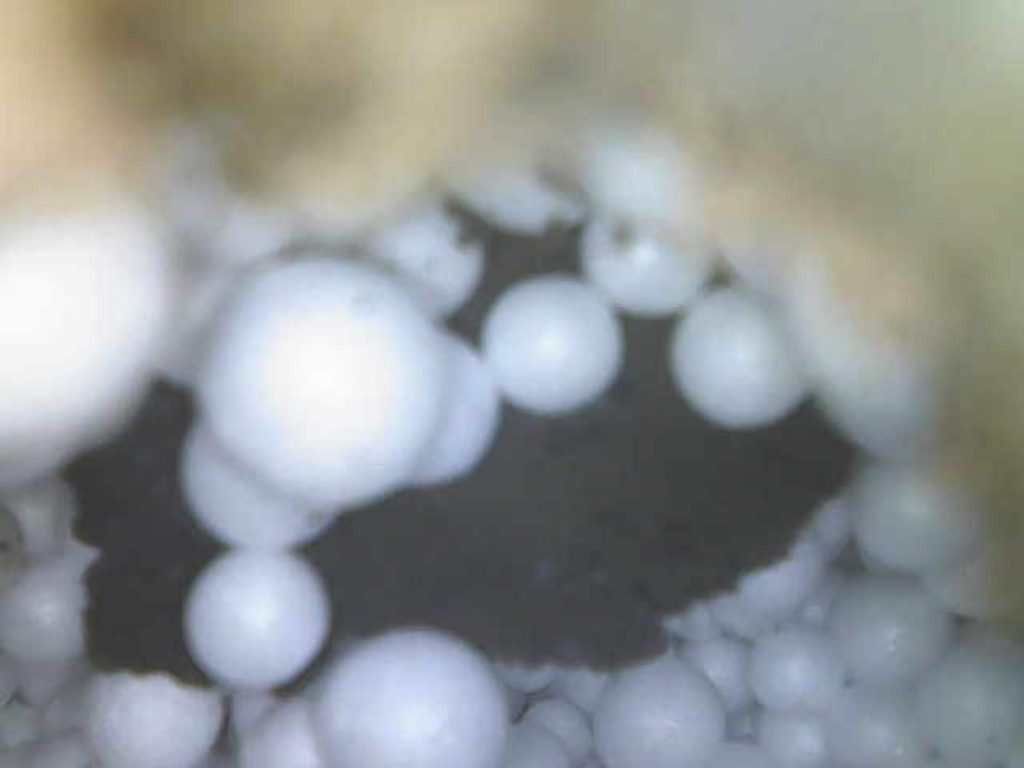
When assessing a property for energy performance, understanding the construction of the walls is a critical element. Walls account for a significant proportion of heat loss in buildings, making their type, construction, and insulation status key factors in determining energy efficiency. For property owners aiming to achieve an EPC rating of C or higher, comprehending the specifics of wall types and how they interact with EPC rating due to building regulations and insulation is essential.
Identifying Wall Types and Construction Methods
The walls of a property can vary significantly depending on the age, construction method, and materials used. Solid brick walls, stone walls, cavity walls, timber frames, and modern insulated systems all have distinct characteristics. Accurate identification of these wall types requires a trained eye and often, specialist tools.
For instance, solid brick walls, common in pre-1920s buildings, tend to have higher heat loss compared to cavity walls, which became prevalent from the 1920s onwards. Stone walls, on the other hand, are often found in older rural properties and can vary greatly in thermal performance depending on the type of stone and construction method. For example, granite and sandstone walls are typically less thermally efficient than limestone or sandstone walls due to their density and thermal conductivity. Correctly identifying the specific stone used in a property can lead to more accurate EPC assessments.
The Role of Building Regulations in Dating Wall Types
Building regulations provide a timeline for understanding construction standards over the decades. Knowing when key regulations were introduced can help surveyors make educated assumptions about the presence or absence of insulation. For example, cavity wall construction began in the late 19th century and became common in general use by the 1920s and 1930s. Insulation in cavity walls, however, only became a standard feature following the introduction of mandatory thermal insulation requirements in the 1976 Building Regulations. These standards were further tightened in the 1980s and beyond. Accurately dating a property and its wall type ensures that assumptions made during an EPC assessment align with historical building practices.
The Importance of a Borescope Inspection
When the construction date or the presence of insulation is uncertain, a borescope inspection can provide definitive answers. This minimally invasive process allows surveyors to inspect inside cavity walls to determine if insulation was present when constructed, has been retrofitted, or if it is absent. This step is crucial for properties where records of insulation work are unavailable, helping to avoid overestimating or underestimating the propertyās energy performance.
Borescope inspections are particularly important for older properties, where retrofitting measures may not always align with modern standards. By gaining a clear understanding of insulation presence and quality of the cavity construction, property owners can better plan upgrades that will have the most significant impact on their EPC rating, and that are appropriate to the building.
Planning for EPC C and Beyond
For property owners planning their path to EPC C, understanding wall types, materials, and insulation status is a foundational step. A detailed survey, including tools like borescope inspections, ensures that investments in retrofitting are targeted and effective. Coupled with an understanding of building regulations and construction timelines, this knowledge allows for more accurate forecasting of the improvements needed to achieve desired EPC ratings.